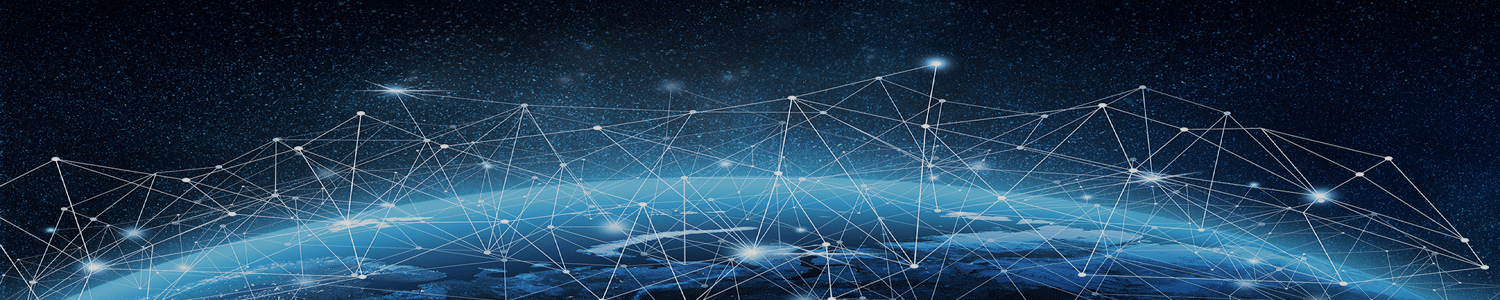
Knowledge Base
Articles
-
The fluoresence of nanodiamond particles is based on color centers incorporated into the diamond lattice. Nitrogen-vacancy centers (N-V) provide red fluorescence and N-V-N (or H3 centers) emit green light. The remarkable property of the color centers in diamond is that they don’t photobleach or photoblink, as compared to quantum dots or organic dyes. In combination with ND’s outstanding biocompatibility, large surface area, and facile surface functionalization, fluorescent NDs (FND) are considered as a new generation of bioimaging probes for the study of cellular dynamics at the single molecular level. Large numbers of N-V centers per particle is desirable for these applications to provide high brightness.
N-V centers in ND posses unique spin properties that render their applications as single photon emitters or ultrasensitive nanoscale magnetometers. For these applications, one N-V center per particle is desirable. NV centers in ND need to be produced. In our approach, NDs manufactured by static high-pressure, high-temperature (HPHT) synthesis and containing about 100 ppm of substitutional N, are irradiated with 2-3MeV electrons and annealed. Other approaches for production of fluorescent NDs are under development in our laboratory.
-
Detonation nanodiamond (DND) is produced from the carbon contained in high-energy explosives. Such explosive compounds simultaneously serve as sources of energy and carbon. The characteristic size of primary particles is ~ 4 nm, which can be isolated from large aggregates formed during synthesis and purification. DNDs contain a wide variety of surface functional groups following purification. As-produced detonation diamond nanoparticles are hydrophilic and can be chemically functionalized for the specific applications listed below. Preliminary investigations determined that DND is non-toxic and biocompatible. Traditional detonation nanodiamond applications include galvanic coatings, polishing pastes and suspensions, polymer composites, lubricating oils, and greases. DND had also been employed for seeding substrates used in the CVD growth of diamond films. New and novel applications of nanodiamond are developing rapidly in fields as diverse as magnetic recording, medical, biomedical and antifouling. Studies indicate that DND is non-toxic and biocompatible, which makes it attractive for medical and biapplications taking into account its rich surface chemistry that can be modified in a controllable way.
-
Natural Diamond
Natural diamond consists of any diamond formed as a result of naturally occurring processes or events. Within the natural diamond classification, two major sub-classifications can be identified, which we will refer to as terrestrial and impact diamond.
Terrestrial diamond is formed within the Earth’s mantle (~100 miles below the surface) where incredible temperatures and pressures can facilitate the formation of diamond from carbon material. These diamonds are transported to the surface via volcanic transport, and are typically found within the mineral Kimberlite. Mined natural diamonds are primarily sourced from Kimberlite.
Impact diamond is formed as a result of meteoric impact events, and can be found within the craters of impact sites. The high temperatures and pressures of the impact can facilitate the formation of diamond. One interesting mineral resulting from impact events is Lonsdaleite (or hexagonal diamond), which is a particularly unique allotrope of carbon with a different crystallographic form as compared to traditional cubic diamond.
Synthetic Diamond
Synthetic diamond consists of diamond grown via human developed methods. The development of synthetic growth methods for diamond were impactful innovations within the mid to latter-half of the 20th century, creating revolutionary materials development in several industries, such as the oil and gas, cutting and abrasive, end electronic industries, among others. Three of the primary sources for synthetic diamond that have been developed are high-pressure high-temperature (HPHT), detonation, and chemical vapor deposition (CVD). With respect to nanocrystalline diamond and fluorescent nanodiamond production, diamond of detonation or HPHT origin are the most important.
High Pressure High Temperature (HPHT) synthetic diamond is produced inside of high pressure (few Gigapascals) and high temperature (~3000 °C) cells which mimic the conditions of natural diamond growth (albeit much more controlled). In these cells, high purity graphite is transported through a molten metal catalyst (e.g. Nickel) to a diamond seed crystal where nucleation and subsequent growth of diamond will occur. Generally, particles on the order of several tens of microns to several hundreds of microns can be grown with the HPHT method. The biggest industrial use for HPHT diamond is in the preparation of highly wear resistant abrasive cutting or drilling components; however, HPHT diamonds are currently the primary source material for preparation of fluorescent diamond (for reasons which will be made clear in a moment).
Detonation Nanodiamond (DND) is formed in the extreme conditions that exist within the first few microseconds of an explosion. No, detonation diamond does not refer to diamond formed from detonating larger diamond particles to fragment them to smaller particles, instead, it refers to diamonds formed from the carbon contained explosives themselves. Explosives such as mixtures of TNT and RDX are detonated within a seal chamber, with cooling provided by gas, liquid, or even from ice in some cases (where the explosive charge is frozen within a block of ice before detonation). The high pressure and temperature experienced in the first few microseconds of the explosion caused the carbon contained in the explosives to convert to a liquid phase, and as the liquid cools, the carbon precipitates out as ~4-5 nm relatively spherical diamond particles. Many of the 4-5 nm “primary particles” often aggregate together, hence why detonation diamond is usually referred to as an “aggregate” size, unless the material has been sufficiently processed to isolate the 4-5 nm primary particles.
Chemical Vapor Deposition (CVD) Diamond is formed in special growth reactors at high temperature (but much lower pressure as compared to the HPHT or detonation techniques). The growth of diamond is initiated on a substrate containing seed diamond crystals using, typically, a mixture of methane (CH4) and hydrogen (H2) gas. CVD diamond and the methods of growing are extensions of growth methods used for many materials in the semiconductor industry; however, the reactors used for the growth of CVD diamond are distinctive from traditional CVD reactors (which will not be discussed here). CVD diamond allows for the most controlled growth of very atomically pure diamond, but it is not a scalable method of production for nanocrystalline particulate diamond. Nevertheless, CVD is an excellent means to produce thin film diamond for microelectronic applications, and it can be used to produce larger gem quality diamonds.
Type Classification of Diamonds
The most established scientific classification system of diamond relates to their either natural or synthetic origin, but to their nitrogen impurity content. Nitrogen is perhaps the most important impurity constituent in diamond because of the dramatic effects it can have on the optical appearance and fluorescence properties. It should be noted that the term ‘impurity’ in this sense means ‘not carbon’ and does not implicitly mean the presence of the nitrogen is an unwanted contaminant (in some cases, this may be true, but in other cases, it may not be). The two major type classifications are:
Type I: Diamond which contains Nitrogen as its primary impurity constituent.
Type II: Diamond which contains almost no measurable nitrogen impurities.
Within the Type I classification:
Type Ia: Diamond containing approximately 0.1 at.% (~1000 ppm) of substitutional nitrogen impurity content. Almost all natural diamonds are of Type Ia.
Type Ib: Diamond containing approximately 0.01 at.% (~100 ppm) of substitutional nitrogen impurity content. Most HPHT diamonds are of Type Ib.
Similarly, the Type II classification contains two sub classifications (Type IIa and Type IIb); however, they are not currently utilized in the production of fluorescent nanodiamonds. Most CVD synthetic diamond is of Type II, and contains less than 0.005 at.% (<50 ppm) of nitrogen impurities. The presence of boron is used to determine the distinction between Type IIa and Type IIb, with Type IIa being the most atomically pure diamond.
Videos
What is Fluorescent Nanodiamond?
What is Nanodiamond?
Fluorescent Nanodiamond Applications
Recent Developments
Practical Tips
-
The high refractive index of diamond causes a substantial amount of light scattering, which can significantly affect the emission spectral profile. Moreover, scattering is maximized at 90 degrees, and it is minimized at 180 degrees. Collecting emitting light at 90 degrees relative to the excitation is pretty standard in most instruments and this obscures spectra collection. Thus, regarding the emission spectra, it is more of an instrument/measurement geometry issue. A measurement angle of 90 degrees typically will not work well with diamond without some additional modifications. We obtained a recommendation for measurements with our Horiba instrument to overcome high light scattering by nanodiamonds: “It proved quite easy to drop the background scatter by using a Fluorolog3 with two double grating monochromators.”
For obtaining emission spectra in our set up, we use a 532 nm laser excitation which is fed into an epifluorescent microscope. In this setup, the collection angle (relative to the excitation line) is at 180 degrees.
-
Detonation nanodiamonds don't agglomerate during storage, but will agglomerate if added to ionic liquids and polymers unless their surface is specifically functionalized for stability in the media of interest. One strategy for introducing NDs into a polymer is through an intermediate solvent, which is evaporated when mixing a polymer with NDs. Please keep in mind what solvents are compatible with your polymer. Add the DND solution gradually into hot polymer while stirring and evaporating the solvent. This method allows you to introduce DND into the polymer more uniformly with less agglomeration. It is important to stress the importance of the compatibility of your polymer and solvent. One popular product we have made for introduction into a polymer is 80 nm Hydrophobic DND with Octadecane.
It disperses readily in chloroform, which can be easily evaporated at low temperatures in hot mixtures with polymers (introduce to the mixture while stirring). We ship the product as a powder.
-
Please reference the following document: